Battery system of the future
ELBC – The Global Battery Innovation Conference (elbcexpo.org)
The 16-19 September was the most important European event of the year, organised by ILA and CBI, on the manufacturing and development of lead-acid batteries.
The conference and presentations covered two main topics:
- developments in the batteries currently in production
- and their applicability in ESS solution
I was present as a representative of Blewin and gave a quite successful presentation. The success of the presentation was due to the fact that we presented truly new technological processes and their technical and economic returns that can be measured in concrete figures. Their impact can have implications both for LA battery solutions for ESS systems and for other applications of LA batteries. No other solutions of this or similar nature were presented, and the hint at the "by-product" of the Blewin grid technology, the one-step recycler process, was a particular success.
The aim was to communicate Blewin and our other developments, and to incorporate the technical content and the associated economic benefits into a positive vision of LA batteries. In addition, we have continued to emphasise that it is the least polluting lead processing technology available today, and can therefore be an important element of both the overall requirements of sustainable development and the expectations of the circular economy.
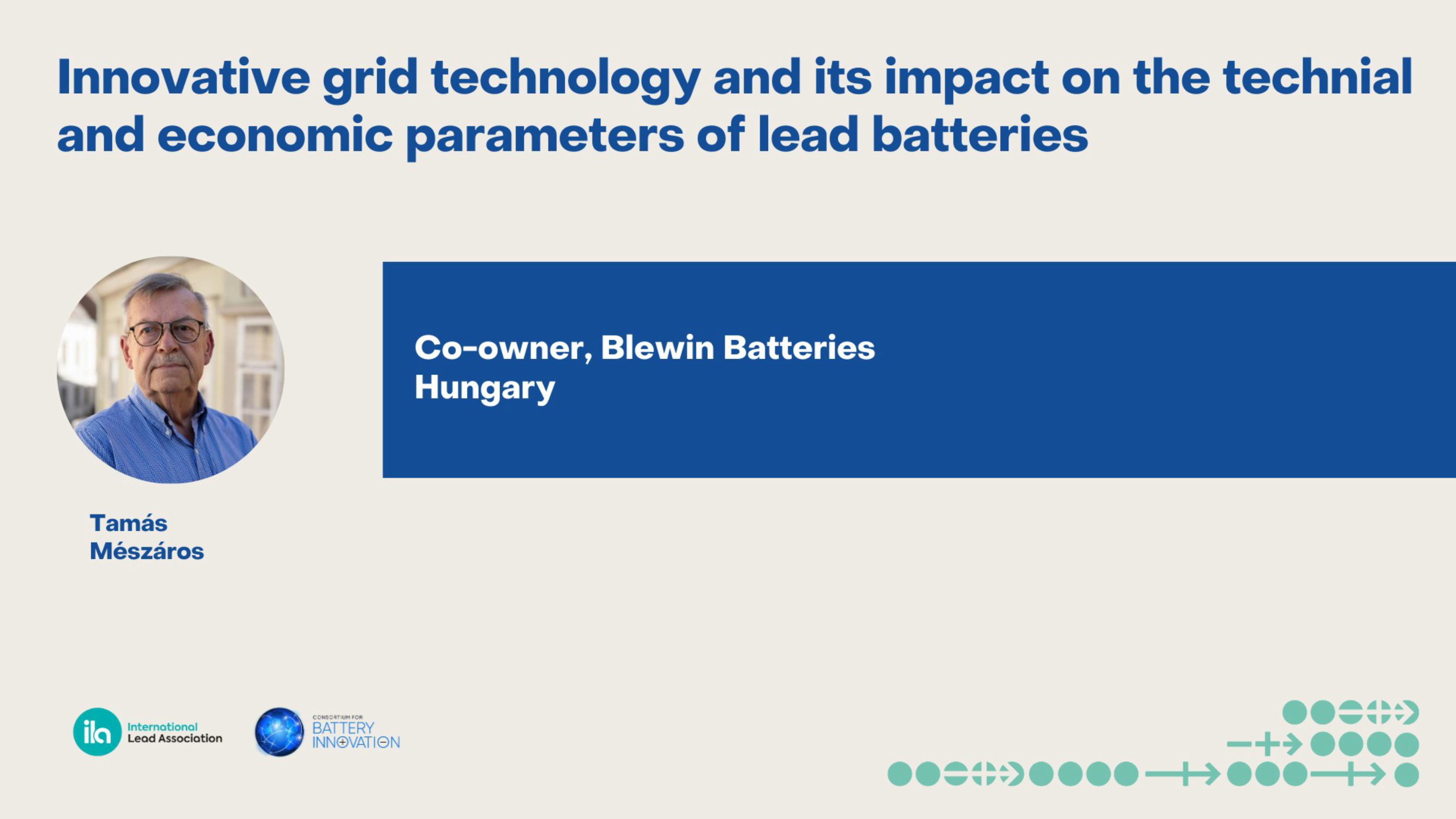
Welcome I am Tamás Mészáros, co-owner of Blewin and developer of other professional knowhow. Since 1996 I have been working on the development of lead grid production technology and, in parallel, on the optimisation of the structure and material of the grids.
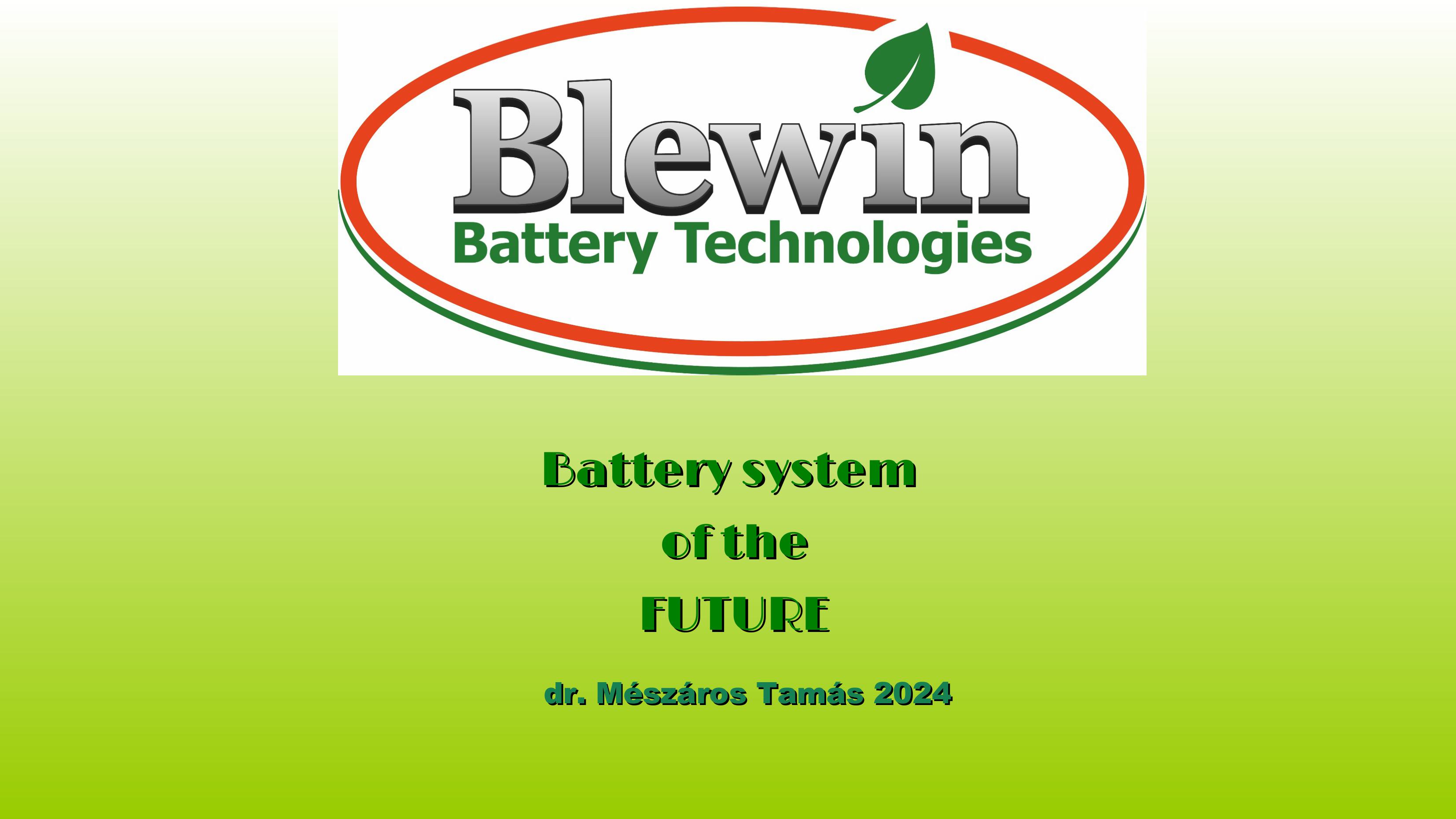
The motto of my work is the subtitle of the following slide (circa 2000, Varta), which I have indicated. Why is this relevant?
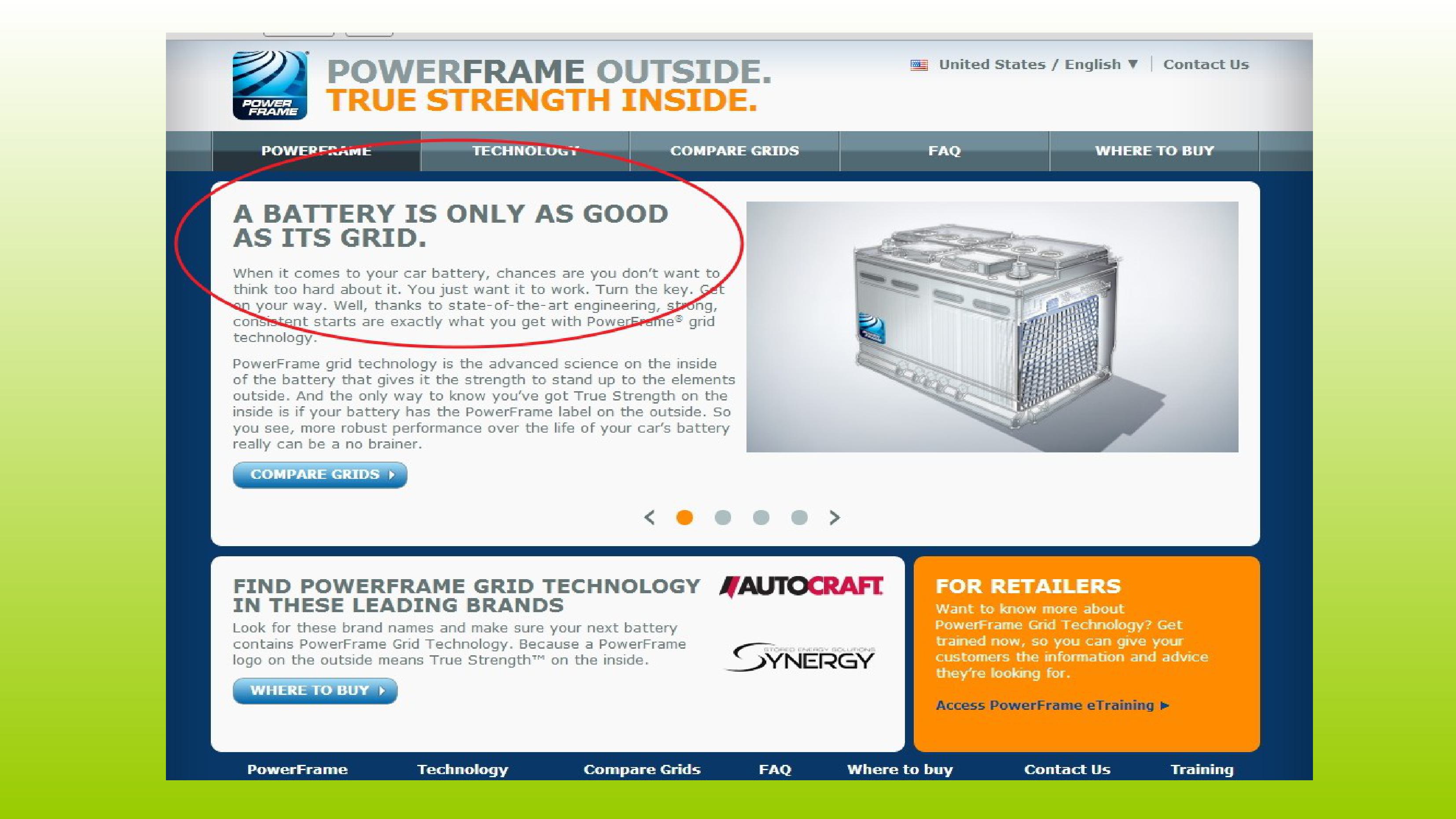
Let's take a look back. What still happens today is that a particular grid manufacturing technology can be used to make grids of a specific material composition and shape, and LA batteries are made from them. The kind we have seen on the market for 70+ years.
To bring the technical needs and some of the societal expectations of today to the surface, it is worth asking: can we follow a different logic? Could we produce batteries that are better suited to today's needs? And if so, what kind of grids are needed, or are there grids that are better suited to this? This development pathway provides answers to these questions.
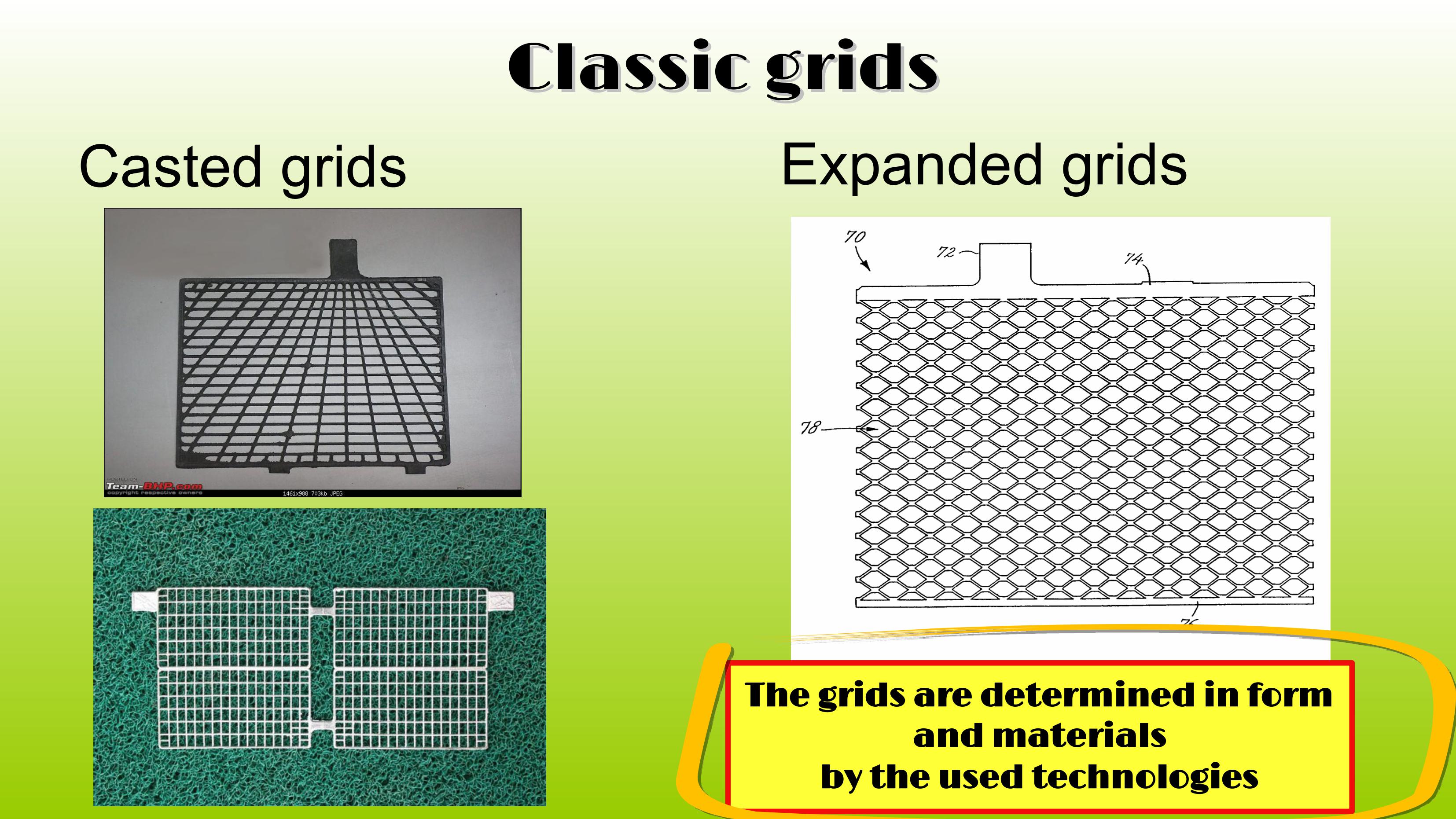
Around 2000, the automotive industry was in the midst of a 42V system fever, for which we developed the right-hand grid type and the 42V battery as an experiment. Comparative measurements showed that at 12 V it was better than the then "star" Optima, so we were on the right track. We know the fate of the 42 V system...
A little later we started to develop the Blewin (Bleigitter Wie Netz) large-scale grid technology and complex battery production system, but unfortunately this ran into the trend generated by other battery systems.
However, as you can see on the right side of the slide, this system can be used to produce any kind of grid from any kind of lead and then treat it. The technology can also be used to produce a grid tailored to the needs of any operating battery factory.
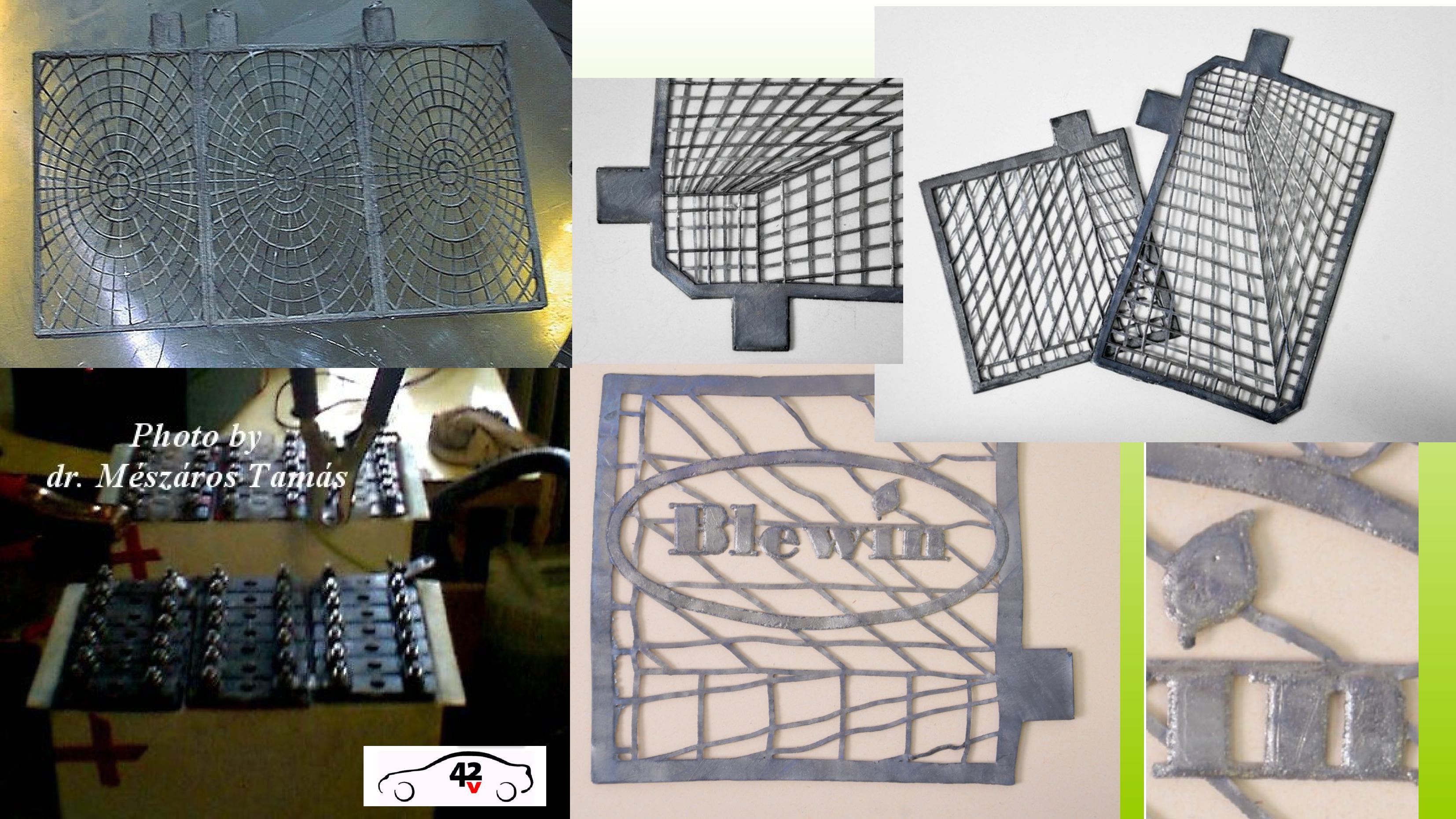
This slide summarises the differences in which this development has made a difference, based on empirical evidence and university measurements. As you can see, there are plenty of them. The combined effect of these is ultimately cca. 30% increase in specific power and weight reduction, with a marked increase in energy density. And the economic benefits (price/value) and environmental benefits are not negligible.
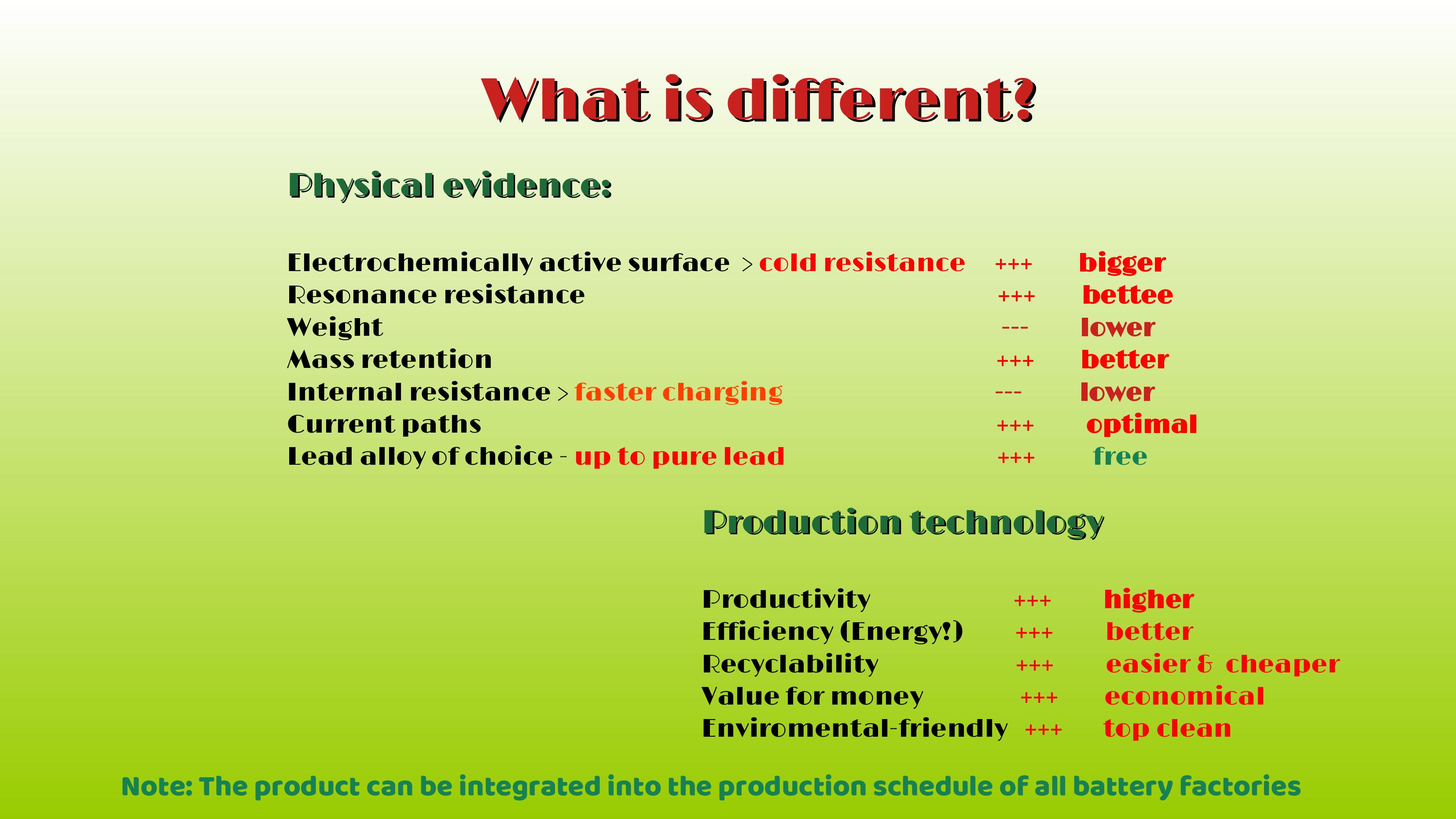
Following the covid, I published the next development step, the Uff (ultra fine fibre) grid crosssection model for the 100 Wh/kg "magic limit" at the BCI Innovation Award in 2022. This was supported by a mathematical model of the design. But beyond the model, the practical feasibility is now ready: with a minimum of improvements to the Blewin machine system, this is technically possible.

To further improve performance in 2023, I slightly modified the concept, as I was motivated by nature instead of drawing structures with a ruler, knowing the efficiency of fractal structures. The Blewin machine system is capable of producing this grid model - with the most favourable crosssections - and making it suitable for use in batteries.
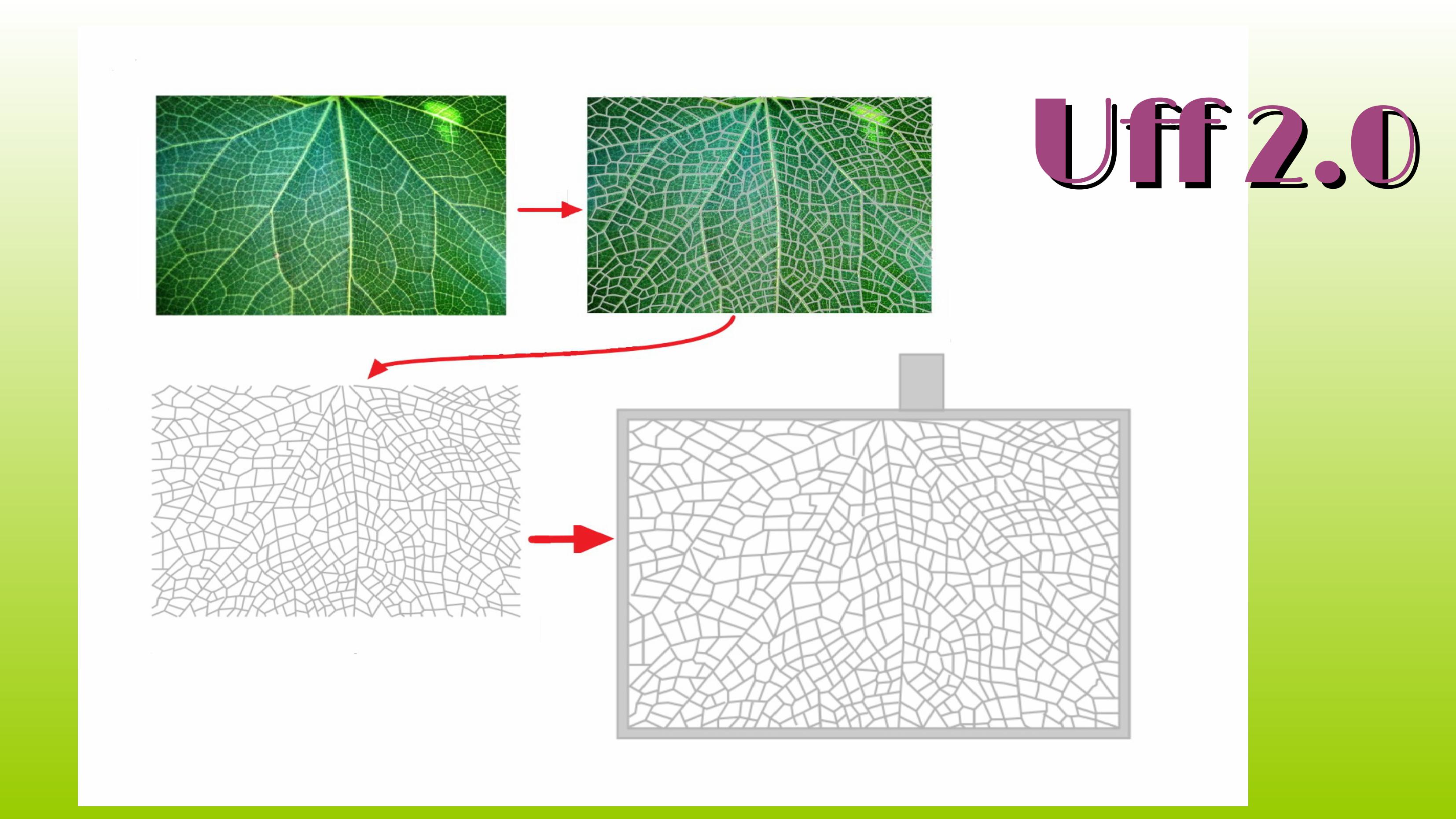
Here, without any scientific explanation, I would like to show the differences based on clear - and real - figures of raw material savings, highlighting also that the Blewin system can process lead with minimal environmental pollution. Here I would also indicate the main uses for which the development path could be particularly attractive.
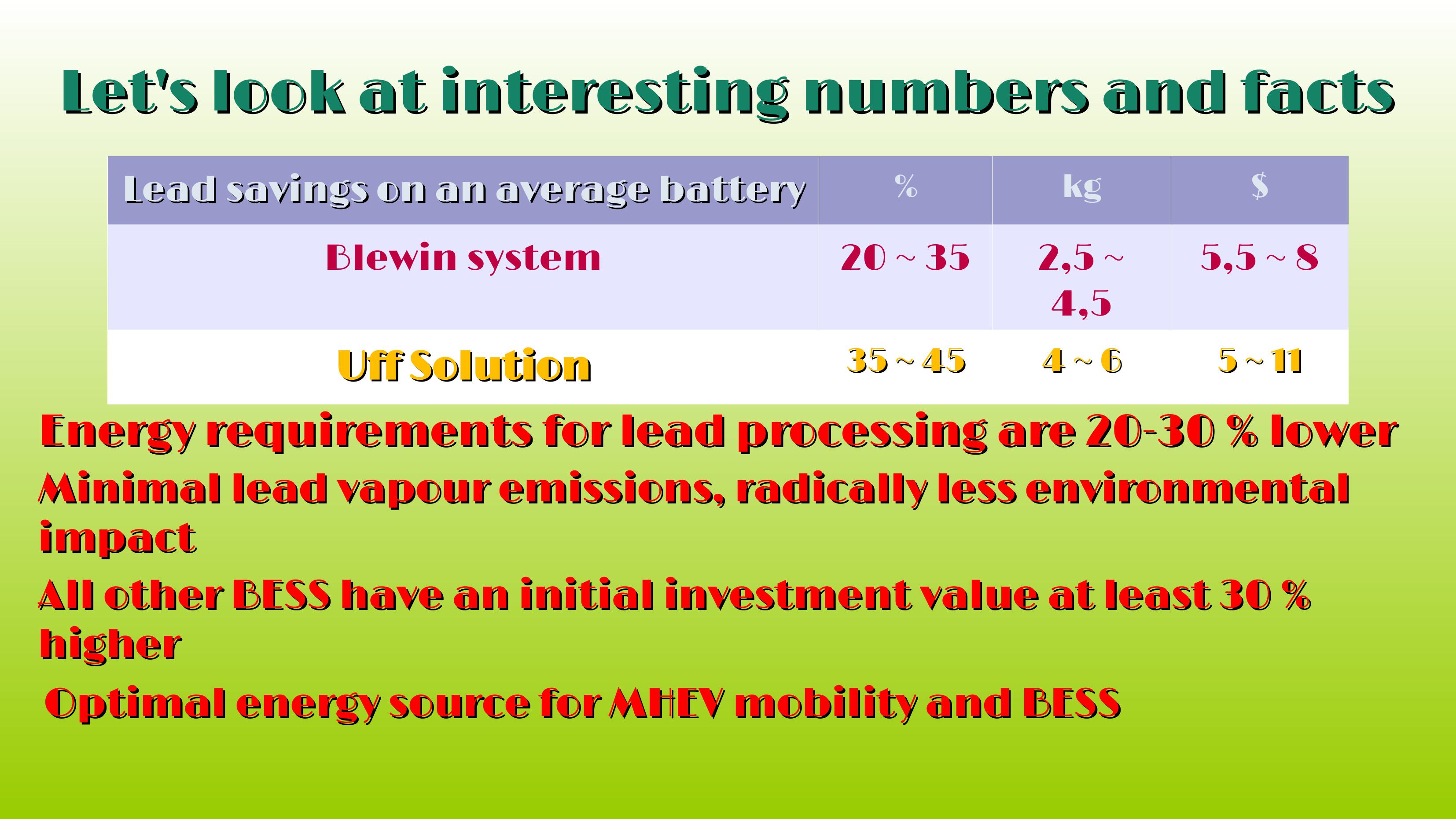
This summary diagram illustrates the effect of the evolution of lead grids - as I have outlined - on specific power. However, in addition to its positive evolution, there are numerous other technical and economic parameters (cycle rate, gypsum deposition rate, charging time and intensity, cold tolerance, cost price) that are also changing (improving), and I cannot go into a detailed analysis of these parameters now, for lack of time, but it is easy to see that their combined benefits are invaluable.
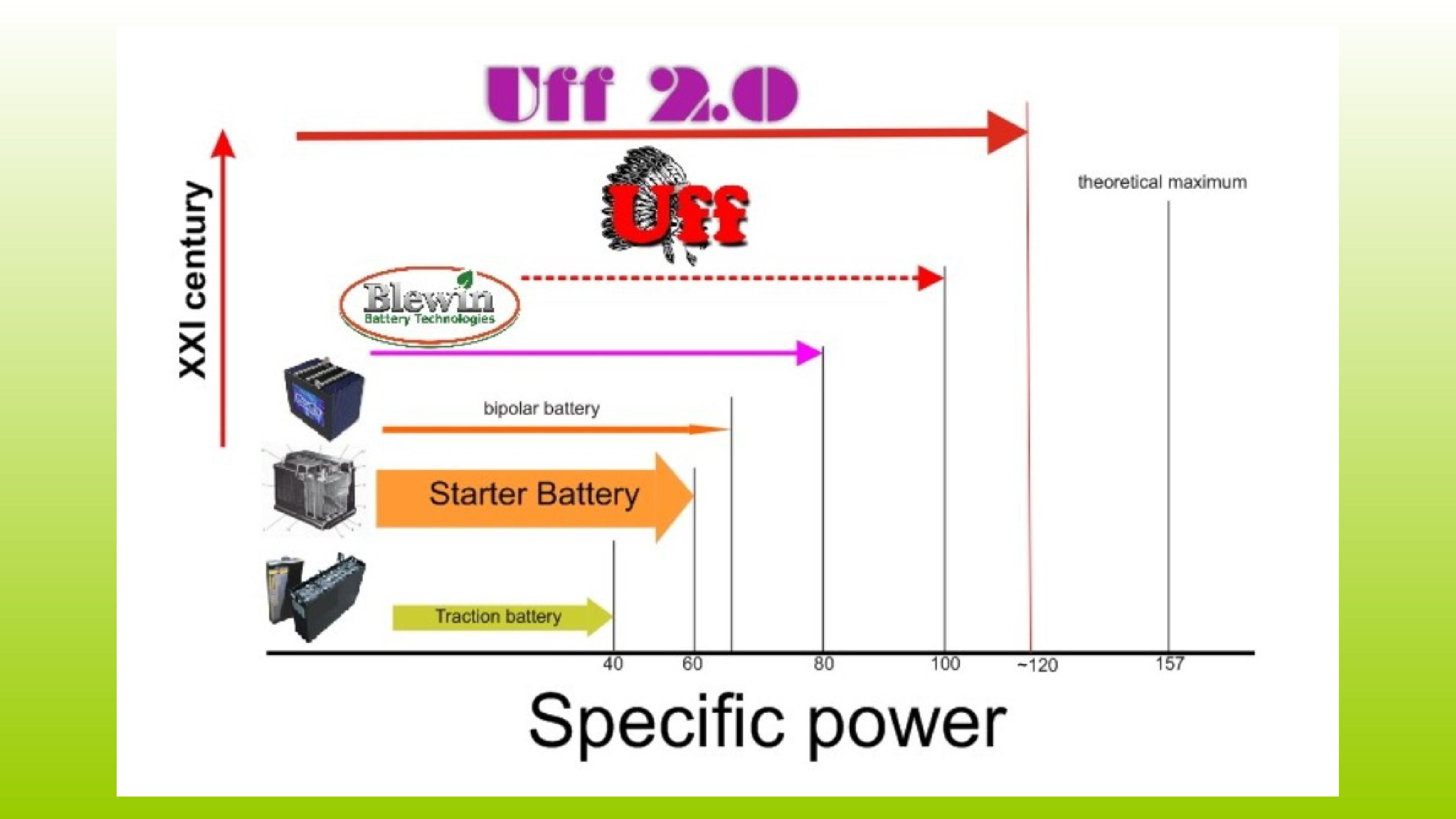
However, I would like to mention the result of a modified version of the Blewin grid machine system, which I presented in 2021 (BCI Inno Award).
This is the Green Lead Project , which is about how molten lead from thermal battery recyclers can be converted in one step directly into lead grids for battery production.
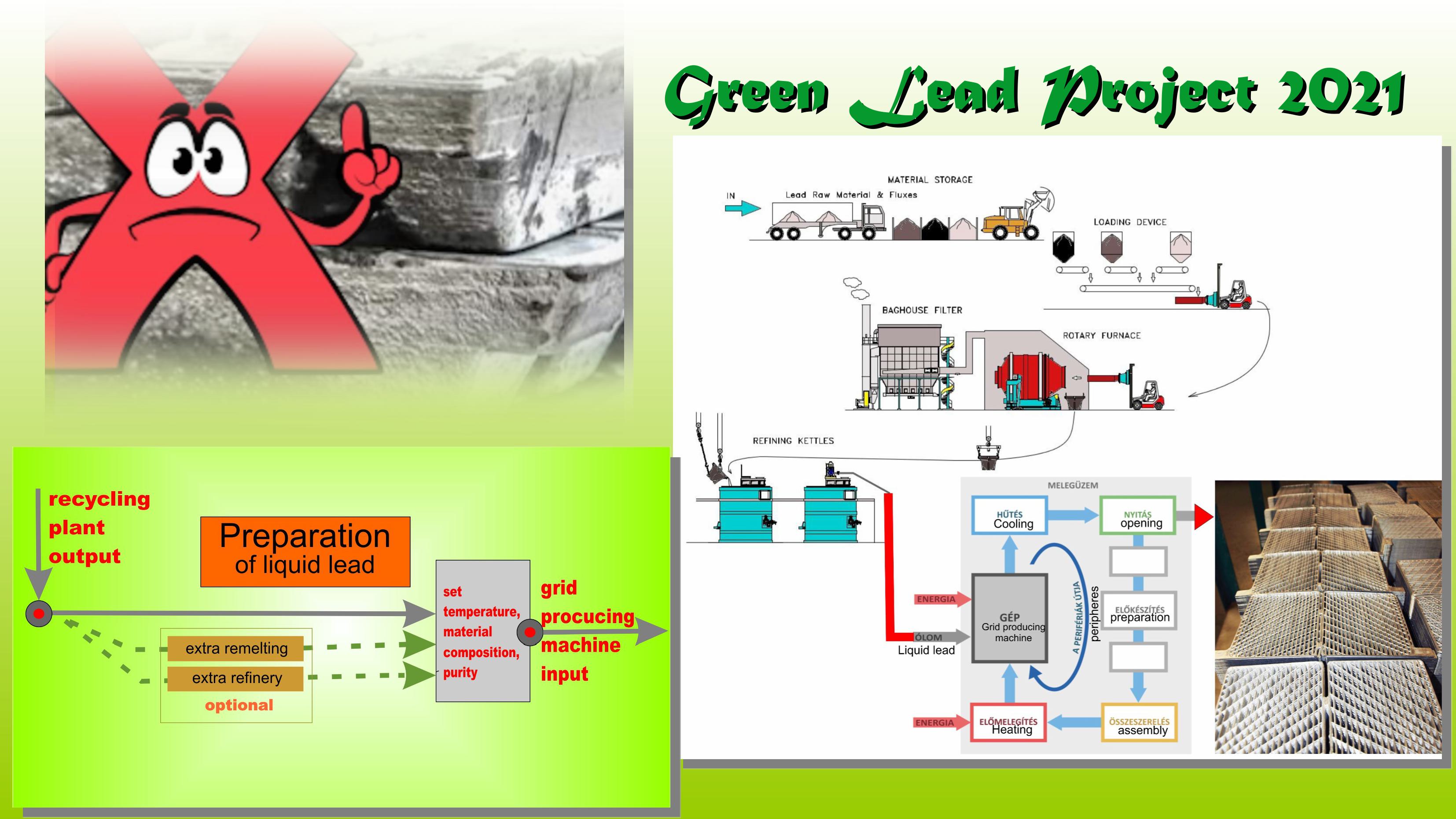
I would like to illustrate the essence and usefulness of this procedure with a set of figures based on statistical data for the year 2022. The framed part shows the amount of energy expense (i.e. essentially wasted) by the US in 2022 in making lead ingots. This is an unreasonable amount. Think about it - the economic and social impact of this is far from negligible.
Is it not worth changing this? The chance is here.
Thank you your attention!
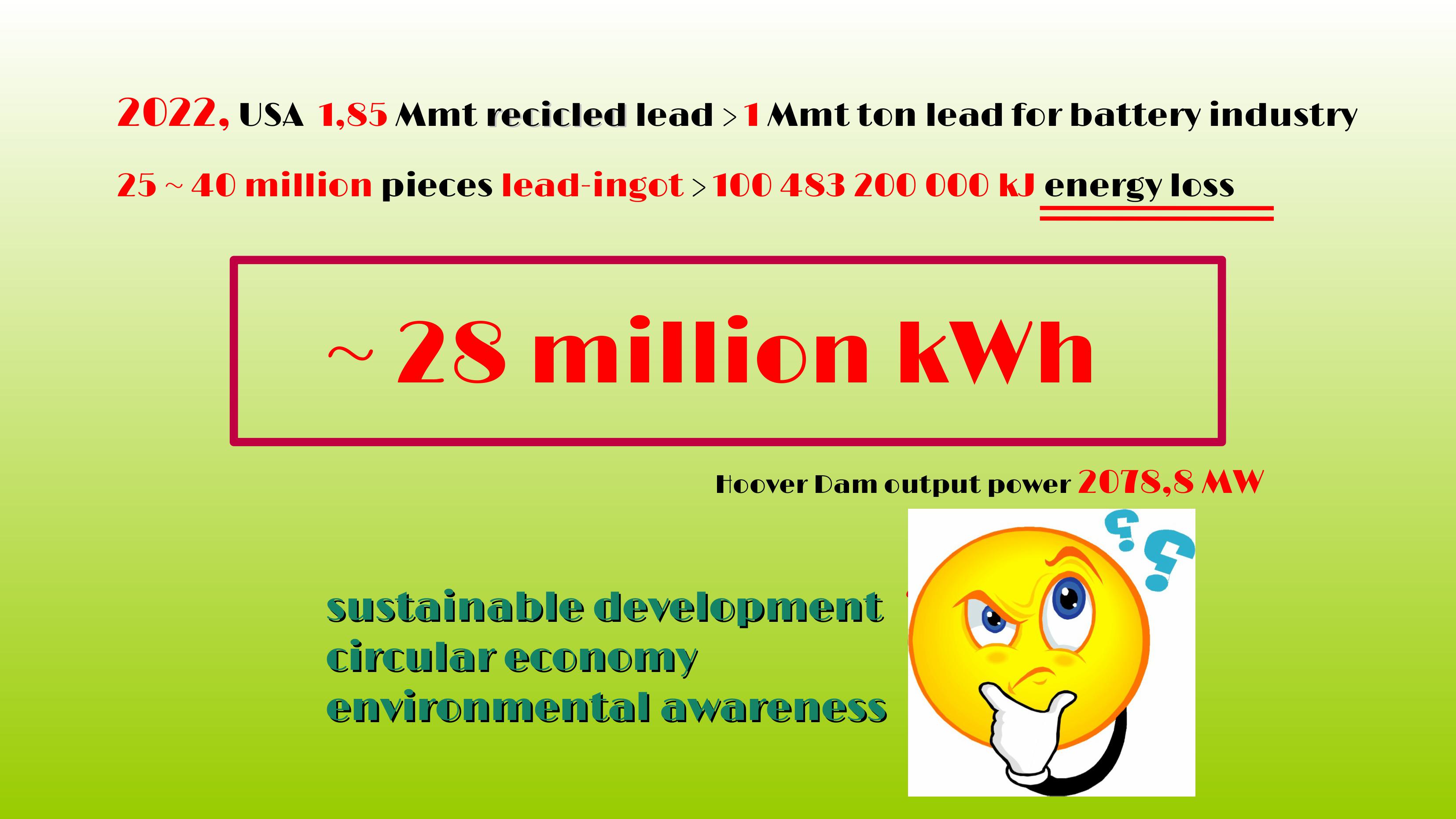
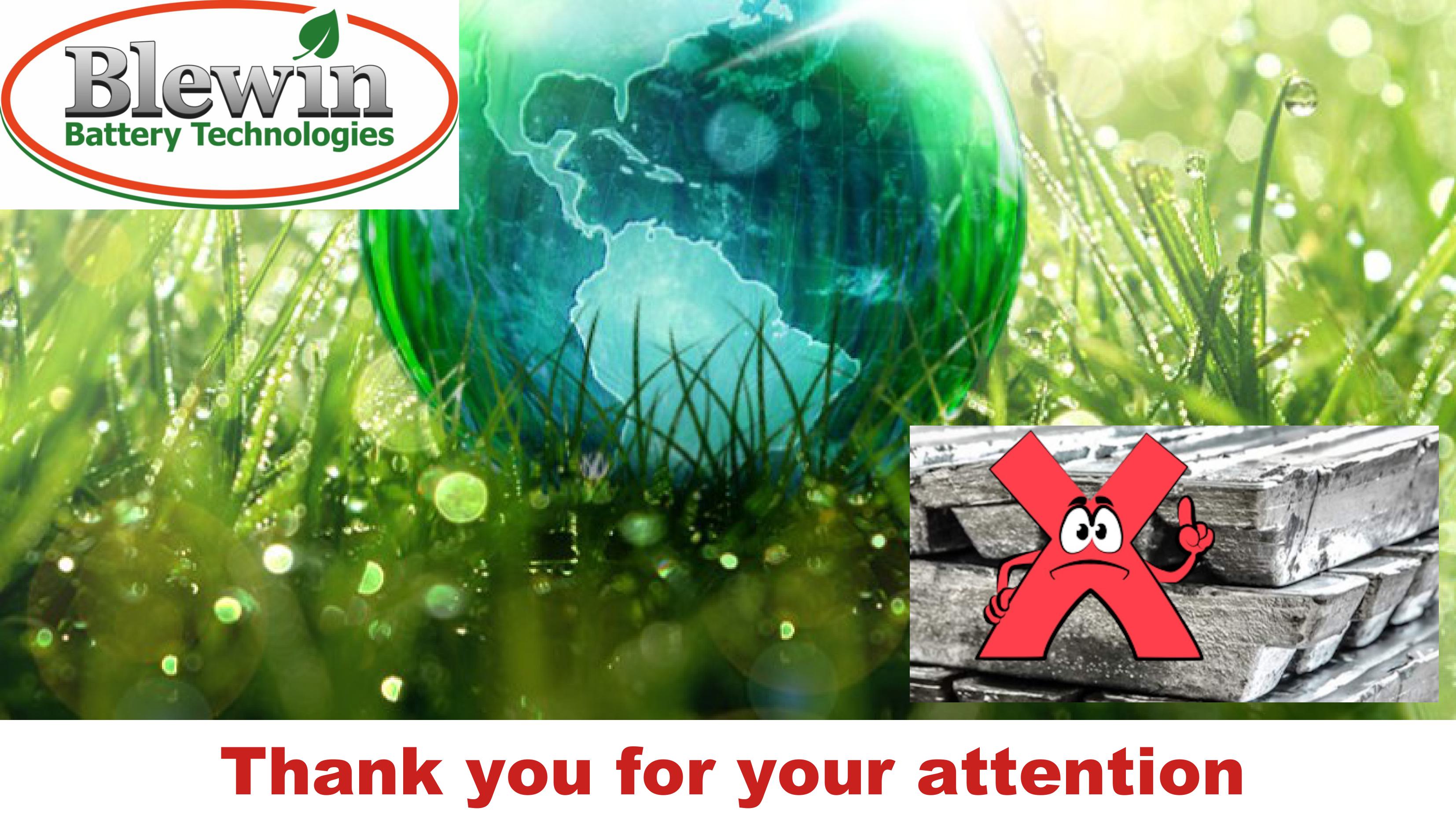